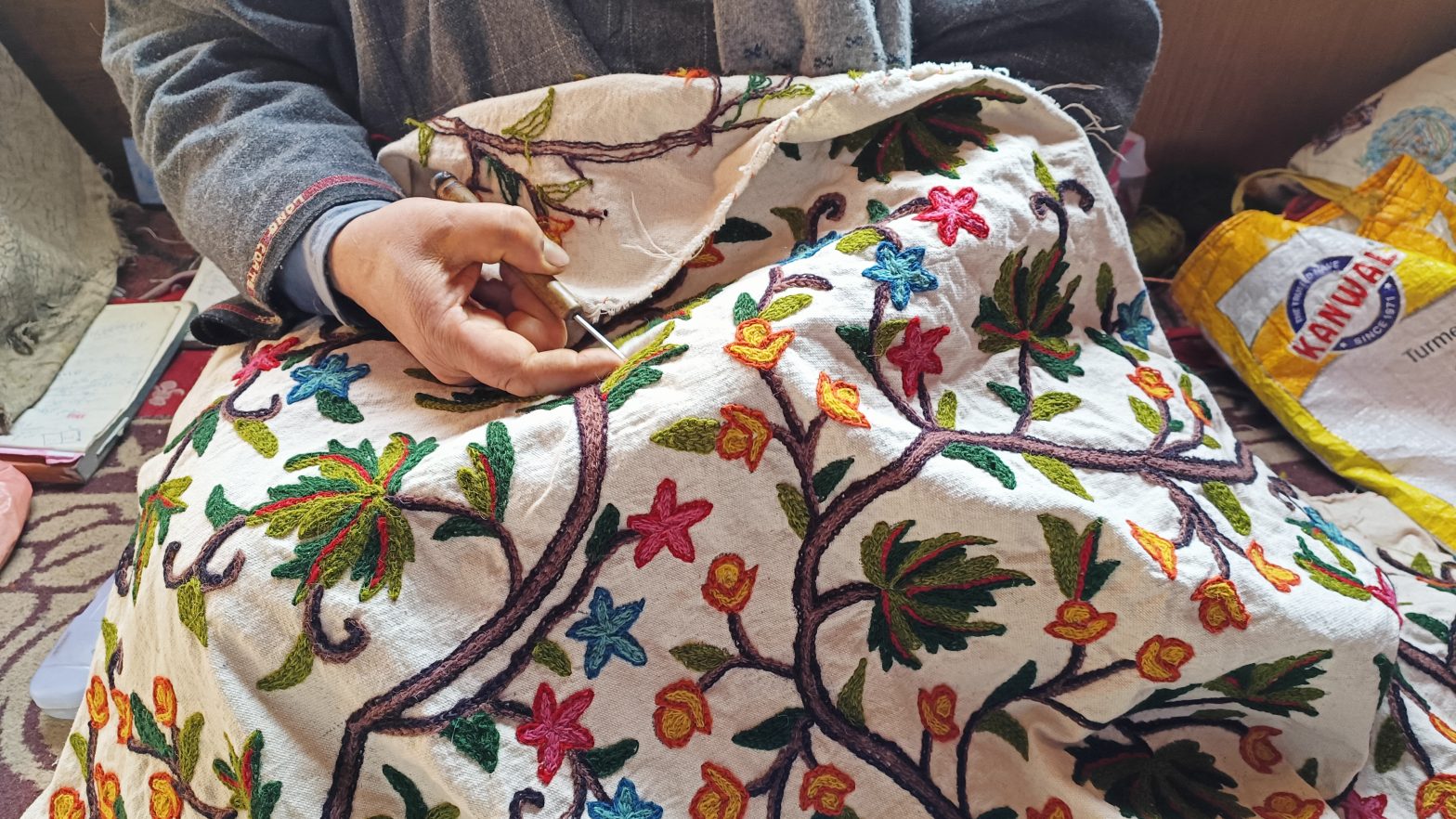
Saving Kashmir’s crewel from machine-made copies
After spurning suggestions to adopt machinery, Gowher Ali Bhat successfully carries on his father’s legacy of crewelwork handicraft, and employs 150 women artisans.
After spurning suggestions to adopt machinery, Gowher Ali Bhat successfully carries on his father’s legacy of crewelwork handicraft, and employs 150 women artisans.
Gowher Ali Bhat rattles out a list of tips on how to distinguish a machine-made crewel curtain from the real, handcrafted thing. He pulls at an embroidered flower and a tuft of woolen thread comes loose. That on an otherwise authentic-looking curtain is a red flag.
“Stitches done by hand with a hook won’t unfasten easily. It takes days for an artisan to complete one curtain,” the 36-year-old said, demonstrating how unscrupulous people are pulling the wool over customers’ eyes by passing off cheaper and inferior factory-made merchandise as handicraft.
Bhat is a second-generation trader of handicraft products that embody the wealth of lavish Kashmiri embroideries such as sozni, zardosi, chain stitch, and crewel work or jalakdozi, as it is called locally.
Also Read | Kashmiri couture trends globally
His store Bhat Chain Stitch in Kadipora of Anantnag district in south Kashmir sells a variety of items – rugs, curtains, bed sheets, cushion covers, totes.
Had I adopted machinery, my artisans would have been unemployed. I can’t do that. They are like my family
His father Ali Mohammad started the business 40 years ago and became part of Kashmir’s cottage industry, which is driven mostly by women who do crewel work and chain stitch with a special hooked needle, called “aari”, on intricate floral and creeper patterns drawn on a cloth held tight by a hoop.
The son joined the trade 15 years ago and confronted the challenge from machine-made copies of his products in the market. It became a life mission for him to save the age-old craft from dying.
“People asked me to take up machinery. I didn’t,” he said.
Bhat is happy that demand for handmade crewel work has rebounded in the past three years, as people have realised the rip-offs are inferior, and don’t last long.
“I am the main wholesaler and retailer of crewel products in south Kashmir. More than 150 artisans are working for me.”
Crewelwork is similar to chain stitch, but distinguished by the two-ply worsted wool yarn called crewel that gives it an embossed 3D effect and adds richness to the textile. Crewel is done on thick material – Kashmiris prefer hessian – popularly used for rugs, drapes, and upholstery.
The process begins with a skilled artisan drawing a design on a perforated sheet of tracing paper. This is called “naqashi”. It could be floral patterns, or animals and humans. The sheet is then laid on cloth, and charcoal powder mixed with kerosene is applied to it.
Also Read | Kashmir’s kani shawl weavers feel left out in cold
After the design gets traced on the fabric, the outlines are sewn with a hook. The thread is normally two-ply worsted wool, but three-ply and silk are also used.
The time taken to complete the artwork depends on the design and the cloth’s size. It can be a day’s work, or take up to two months. The embroidery on Kashmiri crewel products does not cover the entire cloth, which can be between 2×3 feet and 9×12 feet, or more.
The price varies from a few hundred rupees to a good dent in the pocket. Most Kashmiri crewel products are exported, and these are of such high quality that companies would buy and resell them abroad for ten times the price.
But turnovers have been piffling for local artisans because of the cheaper copies in the market. It’s a difficult job, but it is not priced with the real value, said a woman.
“It’s under-priced, if you take into consideration the time and how difficult this job is.”
Scholars credit 15th-century ruler Sultan Zain-ul-Abidin with introducing the craft to Kashmir by inviting a number of craftsmen from Samarkand to train local artisans. It has endured the test of time, but for how long?
People like Bhat are trying to ensure there is another generation of artisans to continue the tradition. “I want to keep this Kashmiri heritage alive. This has been my family’s bread and butter for decades. My heart never allowed me to cheat (by opting machinery),” he said.
He is giving employment to women who would have otherwise remained jobless at home.
Also Read | Kashmir’s willow wickerwork gets a modern facelift
“Had I adopted machinery, my artisans would have been unemployed. I can’t do that. They are like my family,” said Bhat.
Kashmiri handicraft, with its legacy of colour and durable motifs, may have evoked global appreciation, but top buyers say its designers need better branding and market awareness to attract serious money.
The Union territory’s department of handicrafts and handloom has stepped up efforts to prop up crewelwork and chain stitch, including applying this January 10 for their geographical indication (GI) – a sign used on products that have a specific geographic origin, which gives them certain qualities or a reputation, such as Pashmina, and Kashmiri hand-knot carpets.
“More than 10,000 artisans across Kashmir will benefit from the GI certification of their crafts, which have an export potential of more than Rs 200 crore,” said handicrafts director Mahmood Ahmad Shah.
The lead image shows a Kashmiri artisan doing chain stitch embroidery with a hook, called Ari in Kashmiri. (Photo by Aamir Ali Bhat)
Aamir Ali Bhat is a journalist and independent researcher based in Kashmir. He writes on human rights violations, politics and the environment.