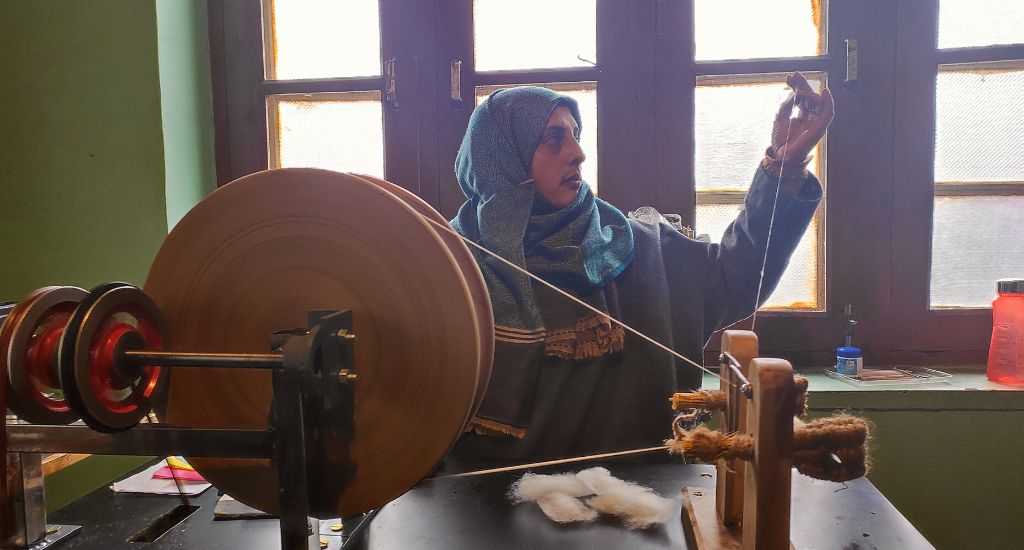
Why Kashmiris love to spin a yarn
Kashmir has reinvented the old wooden spinning wheel into a new machine to yarn Pashmina wool, making the craft both – comfortable and profitable.
Kashmir has reinvented the old wooden spinning wheel into a new machine to yarn Pashmina wool, making the craft both – comfortable and profitable.
The wheel of fortune turned full circle for a Kashmiri single mother of two when a timeworn and time-intensive spinning machine that she had thrown away nine years ago returned to her home in a new avatar and brought renewed hope of financial stability.
The redesigned spinning wheel that works by a foot pedal to yarn wool from the Pashmina goat sits in a corner of 45-year-old Zubaida Bano’s modest house in Zakura village on the outskirts of Srinagar. And she can’t get enough of this charkha fixed on a table – resembling a sewing machine.
She and many Kashmiri women like her had for years spun raw Pashmina and Shahtoosh wool into threads on a traditional wooden spinning wheel, called yinder in Kashmiri.
They would sit cross-legged for hours on the floor, hunching over the yinder, and it took them about two months to yarn enough wool for a single Pashmina shawl. Plus, prolonged use gave them a chronic backache.
Their job was backbreaking, but the income was meagre.
Zubaida was among many who traded the yinder for livelihoods that paid better, although six centuries of tradition dictated that threads for the world’s finest and most expensive cashmere were homespun in the old-fashioned way.
By the turn of this millennium, most yinders were abandoned in attics or sold as scrap.
A time came when only a handful of households continued with the age-old craft of spinning yarn for the highly-prized cashmere, which takes its name from Kashmir, where artisans weave the wool into exquisite shawls that cost hundreds of dollars apiece in world fashion capitals.
“We couldn’t make ends meet with our paltry earning of Rs 30 to Rs 40 a day from the outdated yinder. So, I shifted from kataen kaem (hand-spinning of yarn) to other jobs almost 13 years ago,” said Shaista Bilal, who is also 45.
But deep within, the woman from downtown Srinagar yearned to go back to the craft she learned from her mother.
“Fortunately, I came to know about this new yinder, got a few days of training, and now I am able to earn about Rs 250 to Rs 300 a day,” Shiasta said.
A group of scientists from Sher-E-Kashmir University of Agricultural Sciences and Technology of Kashmir (SKUAST-K) put their heads together to give the yinder a modern spin. Out of this brainstorming was born the new, easy-to-operate machine, which was introduced last year.
It almost doubled the output, as it freed up both hands of the person, who had to earlier pull the thread with one hand and rotate the charkha with the other.
Dr Sarfaraz Ahmad, who was a part of the SKUAST-K team, said the new yinder is a healthier option, and faster and comfortable too.
“Women use this machine sitting on a chair (which they couldn’t do with the old one),” he said.
The women these days earn Rs 2.5, the government-fixed price for each knot of thread comprising a band of about 10 strands, 10cm in length. They can make many knots with the new spinning wheel, thereby earning 200% to 300% more than what they used to with the outmoded yinder.
The scientists’ approach was singular: to bring skilled women like Zubaida and Shiasta back into the Valley’s Pashmina sector – a major handicraft export industry, which was struggling to keep afloat because of the influx of mechanized shawls, ban on Shahtoosh, inflation and other headwinds.
“This pedal-driven charkha helped increase output of hand-spun Pashmina yarn. We have trained almost 200 women, and young girls too, to operate the new yinder,” said Ishfaq Qadri, owner of Me & K Pashmina House in Srinagar, a store where he also runs a training centre.
Qadri had donated more than 40 modern yinders to the women yarn-makers, who are an important cog in the wheel for industry. “Such technological interventions are definitely necessary and helpful for the revival of the Pashmina industry,” he said.
For the uninitiated, Pashmina is wool from the eponymous goat that inhabits the icy heights of Changthang in Ladakh, while the soft underfur of Chiru antelopes is called Shahtoosh, which means “king of wools” in Persian, and considered the warmest natural fibre in the world.
Pashmina and Shahtoosh shawls are renowned for providing enveloping warmth while being thin enough to be pulled through a finger ring. Both products are heritage heirlooms of Kashmir.
Shahtoosh, which once formed part of a wealthy bride’s trousseau, was banned in the early 1990s as the antelope that wanders the vast and inhospitable terrain of the Tibetan plateau was almost wiped out by hunters.
A single antelope yields only about 150 grams of wool and a single shawl requires about 340 grams, meaning three Chirus must be killed for every shawl.
Pastoral nomads living in the inhospitable Chunghthang terrain herd the famed and hardy Pashmina goats and supply the ultrasoft fur. Demand for Pashmina, which is painstakingly combed from the goats, sorted, cleaned and hand woven, has always outstripped supply.
The lead image at the top shows a woman tries her hands at the new yinder at a training centre in Srinagar (Photo by Nasir Yousufi)
Nasir Yousufi is a journalist based at Srinagar.